Quality Assurance
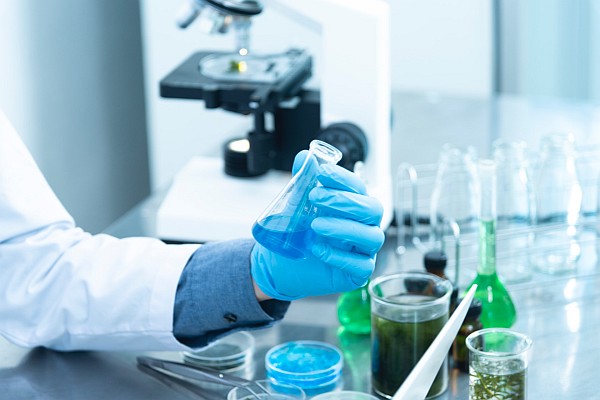
“High Quality” standard is the utmost important and integral part of our work culture at CRESCENT LABS. We believe in blending human skills with technology in giving our customers a visible edge in its market domain by maintaining high efficiency levels in procurement, planning, production, warehousing, and supply – infused with assured quality and complete transparency at each stage of business.
Our QA/QC systems are focused keeping in mind the ever-changing needs of the Pharmaceutical Industry; and are designed to produce goods of the highest quality, efficacy, and safety. These systems are guided by our strict internal Quality Policy and within the framework of cGMP norms of The World Health Organization and local statutory requirements.
Technical and Quality Audits are carried out at regular intervals to ensure that Total Quality Management (TQM) is practiced at each stage of storage, handling, manufacturing, packing and testing of Bulk, Intermediate and Finished Products as per the SOPs and pre-determined Specifications laid down by our Quality Department. Each process is further Validated as per the Validation Master Plan (VMP) and documented for retrieval as demanded. This system gives an edge to our customers who have a Quality centric approach in their patented manufacturing processes.
All products are manufactured in compliance with WHO-GMP guidelines in designated and pre-qualified Clean-Rooms, with adequate controls of Air Handling Units (AHU’s) to prevent cross-contamination and designed to maintain the Class of Area as specified under Schedule ”M” of Drugs and Cosmetics Act 1948 and cGMP requirements as per the guidelines of WHO; with the use of state-of-the-art technology and equipment, under the supervision of highly trained and qualified staff.